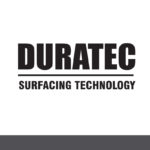
Website Dura Technologies, Inc.
Dura Technologies is looking for a Manufacturing Office Clerk. This position requires a friendly disposition, excellent phone and interpersonal skills, rapid responsiveness, intermediate computer skills, able to prioritize multiple tasks, and the ability to work quickly while maintaining quality and accuracy. This position will represent the company in an outgoing and professional manner and may be the first point of contact and liaison between customers and Management.. The position is responsible for managing and routing calls to the various departments. At times the work is highly confidential, challenging and will include proofreading, general communication, and receiving/responding to phone and email communication.
ESSENTIAL FUNCTIONS:
· Professional phone etiquette in answering all incoming calls and routing all calls to the appropriate parties
· Provide customers with order updates and/or delivery status on order(s); in conjunction with the GM and the Production Manager
· Strong communication skills – written, verbal, interpersonal
· Ability to work with and maintain highly confidential information
· Process orders and provide information on our products and services to our customers/representative
* Strong problem-solving and analytical skills
Requirements & Experience:
· Experience working in a manufacturing environment & use of an ERP System
* Experience with heavy incoming phone volume and good interpersonal skills.
· Deadline driven, results-oriented with initiative and a sense of urgency
· Professional telephone presence.
· Requires a knowledge of Microsoft Office (Outlook, Excel, Word, Etc.)
· Self-motivation to seek additional tasks and projects.
· High school diploma required
· Three + years Office Clerk experience preferred
Ability to work effectively within a team and independently
ERP experience; Syspro experience a plus.
Our Benefits Package
- Medical, Dental, and Vision Insurance
- Life Insurance
- 401(k) Plan
- Paid Holidays
- Vacation Time
- Sick Pay
- Referral Bonus Program
Pay
In accordance with California’s labor code, the expected salary/hourly range for this position is between $20.00 and $27.00 per hour. A new hire’s actual pay will be determined based on experience, skillset, geographic location, and other job-related factors.
To apply for this job email your details to Hr@duratec1.com